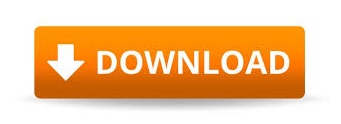
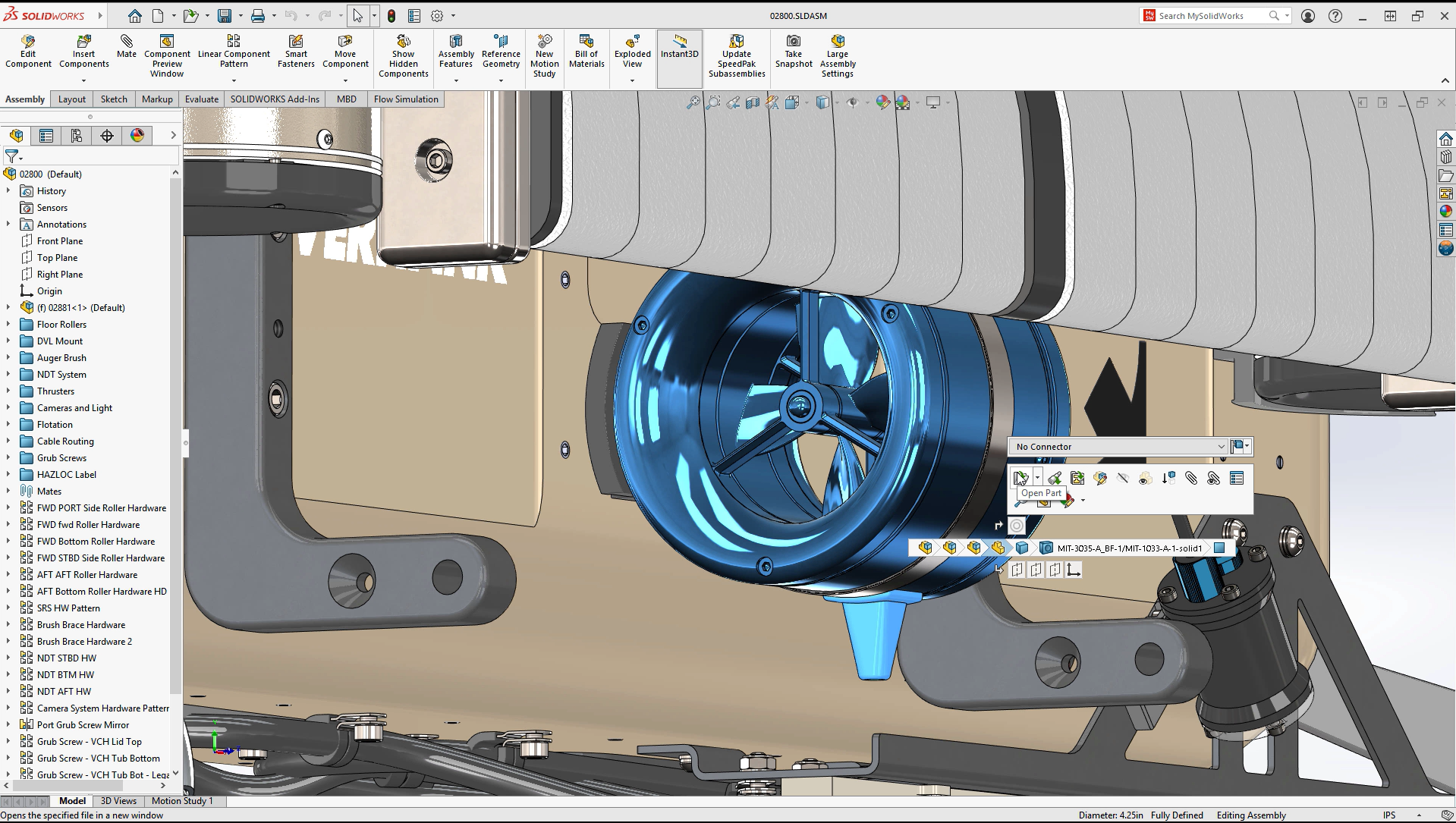
Īdrian Bowyer talking about the RepRap Project at Poptech 2007 The reason given was congestion of the market for low-cost 3D printers and the inability to expand in that market. In early January 2016, RepRapPro (short for "RepRap Professional", and one commercial arm of the RepRap project in the UK) announced that it would cease trading on 15 January 2016. The latest iterations used OpenBeams, wires (typically Dyneema or Spectra fishing lines) instead of belts, and so forth, which also represented some of the latest trends in RepRaps. In 2012, the first successful Delta design, Rostock, had a radically different design. Within two years, RepRap and RepStrap building and use were widespread in the technology, gadget and engineering communities. It was a miniature of Mendel, with 30% of the original print volume. On 31 August 2010, the third generation design was named Huxley. Gada Humanitarian Innovation Prize" for the design and construction of an improved RepRap. On 27 January 2010, the Foresight Institute announced the "Kartik M. Mendel's shape resembles a triangular prism rather than a cube. On 2 October 2009, the second generation design, called Mendel, printed its first part. In April 2009, electronic circuit boards were produced automatically with a RepRap, using an automated control system and a swappable head system capable of printing both plastic and conductive solder. A couple hours later the "child" machine had made its first part: a timing-belt tensioner.įirst part ever made by a RepRap to make a RepRap, fabricated by the Zaphod prototype, by Vik Olliver () On, Darwin achieved self replication by making a complete copy of all its rapid-prototyped parts (which represent 48% of all the parts, excluding fasteners). By September that year, at least 100 copies had been produced in various countries. On 14 April 2008, RepRap made an end-user item: a clamp to hold an iPod to the dashboard of a Ford Fiesta car. On 9 February 2008, RepRap 1.0 "Darwin" made at least one instance of over half its rapid-prototyped parts. On 13 September 2006, the RepRap 0.2 prototype printed the first part identical to its own, which was then substituted for the original part created by a commercial 3D printer. Funding was obtained from the Engineering and Physical Sciences Research Council. RepRap was founded in 2005 by Dr Adrian Bowyer, a Senior Lecturer in mechanical engineering at the University of Bath in England. A preliminary study claimed that using RepRaps to print common products results in economic savings. They intended for the RepRap to demonstrate evolution in this process as well as for it to increase in number exponentially. ĭue to the ability of the machine to make some of its own parts, authors envisioned the possibility of cheap RepRap units, enabling the manufacture of complex products without the need for extensive industrial infrastructure.
#SOLIDWORKS FLOW SIMULATION 2013 DOWNLOAD SOFTWARE#
RepRap is short for rep licating rap id prototyper.Īs an open design, all of the designs produced by the project are released under a free software license, the GNU General Public License. The RepRap project started in England in 2005 as a University of Bath initiative to develop a low-cost 3D printer that can print most of its own components, but it is now made up of hundreds of collaborators worldwide. Adrian Bowyer (left) and Vik Olliver (right) are members of the RepRap project.
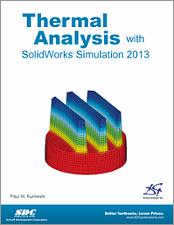
All of the plastic parts for the machine on the right were produced by the machine on the left.
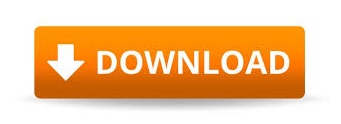